Are you tired of battling escalating material costs, tight deadlines, and the constant pressure to deliver exceptional industrial construction projects? Imagine a world where your building materials not only meet stringent technical requirements but also enhance the aesthetic appeal and long-term value of your factories, warehouses, and shopping centers. Cozydoor introduces the transformative potential of anodized aluminum – a game-changing solution that empowers project managers and directors like you to achieve unprecedented levels of efficiency, durability, and design excellence. Discover how this versatile material can revolutionize your approach to industrial construction.
What is Anodizing and How Does it Work?
Anodizing, a sophisticated electrochemical process, transforms ordinary aluminum into a super-material boasting enhanced corrosion resistance, durability, and aesthetic appeal. This controlled oxidation process thickens the naturally occurring oxide layer on the aluminum surface, creating a protective shield that withstands the harshest environments.
Unlike coatings that simply adhere to the surface, the anodized layer becomes an integral part of the aluminum, ensuring exceptional performance and longevity. Understanding the science behind anodizing empowers you to make informed decisions and harness its full potential for your construction projects.
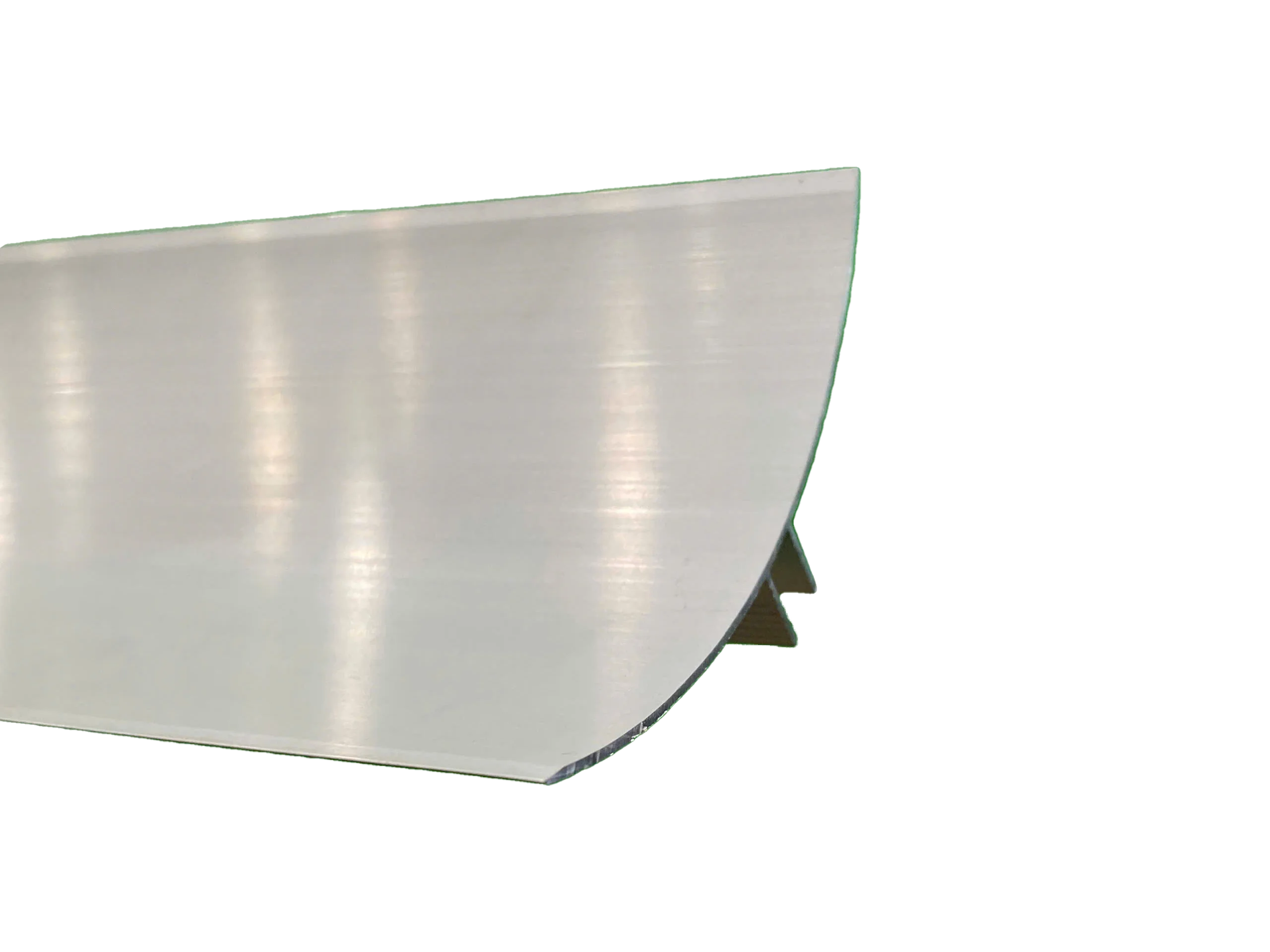
The science behind anodizing: Aluminum Oxidation explained.
Aluminum naturally forms a thin layer of oxide when exposed to air. This oxide layer protects the metal beneath from further corrosion. However, this layer can be enhanced through anodizing, which involves immersing the aluminum in an acid electrolyte bath and applying an electric current. This process thickens the oxide layer significantly, often up to 25 micrometers or more, depending on the type of anodizing used.
Scientific studies have shown that anodized aluminum can withstand harsh environmental conditions without degrading. For instance, research indicates that anodized coatings can resist corrosion for thousands of hours in salt fog environments, making them suitable for coastal applications where exposure to saltwater is a concern.
The electrochemical process: A step-by-step breakdown.
- Preparation: The aluminum surface is cleaned to remove any contaminants.
- Electrolytic Bath: The aluminum is submerged in an acid solution (commonly sulfuric acid).
- Electric Current Application: An electric current is passed through the solution, causing oxygen ions to react with the aluminum surface.
- Oxide Layer Formation: A thick oxide layer forms on the surface of the aluminum.
- Sealing: The porous oxide layer is sealed to enhance corrosion resistance and improve color retention.
This process not only enhances durability but also allows for various finishes and colors, appealing to aesthetic considerations in construction projects.
Types of anodizing and their applications.
Anodizing offers a range of options tailored to diverse project needs.
- Type I anodizing, also known as chromic acid anodizing, produces a thin, decorative coating ideal for applications where minimal dimensional change is critical.
- Type II anodizing, the most common type, utilizes sulfuric acid and creates a thicker, more protective layer suitable for architectural applications and exterior components.
- Type III, or hard anodizing, produces an exceptionally hard and wear-resistant surface, perfect for high-performance applications in demanding environments.
Understanding these distinctions allows you to select the optimal anodizing type for your specific project requirements.
Advantages of Anodized Aluminum
Cozydoor’s anodized aluminum offers a compelling array of advantages that directly address the challenges faced by construction professionals. From enhanced durability and corrosion resistance to improved aesthetics and cost-effectiveness, anodized aluminum emerges as the ideal material for demanding industrial construction projects.
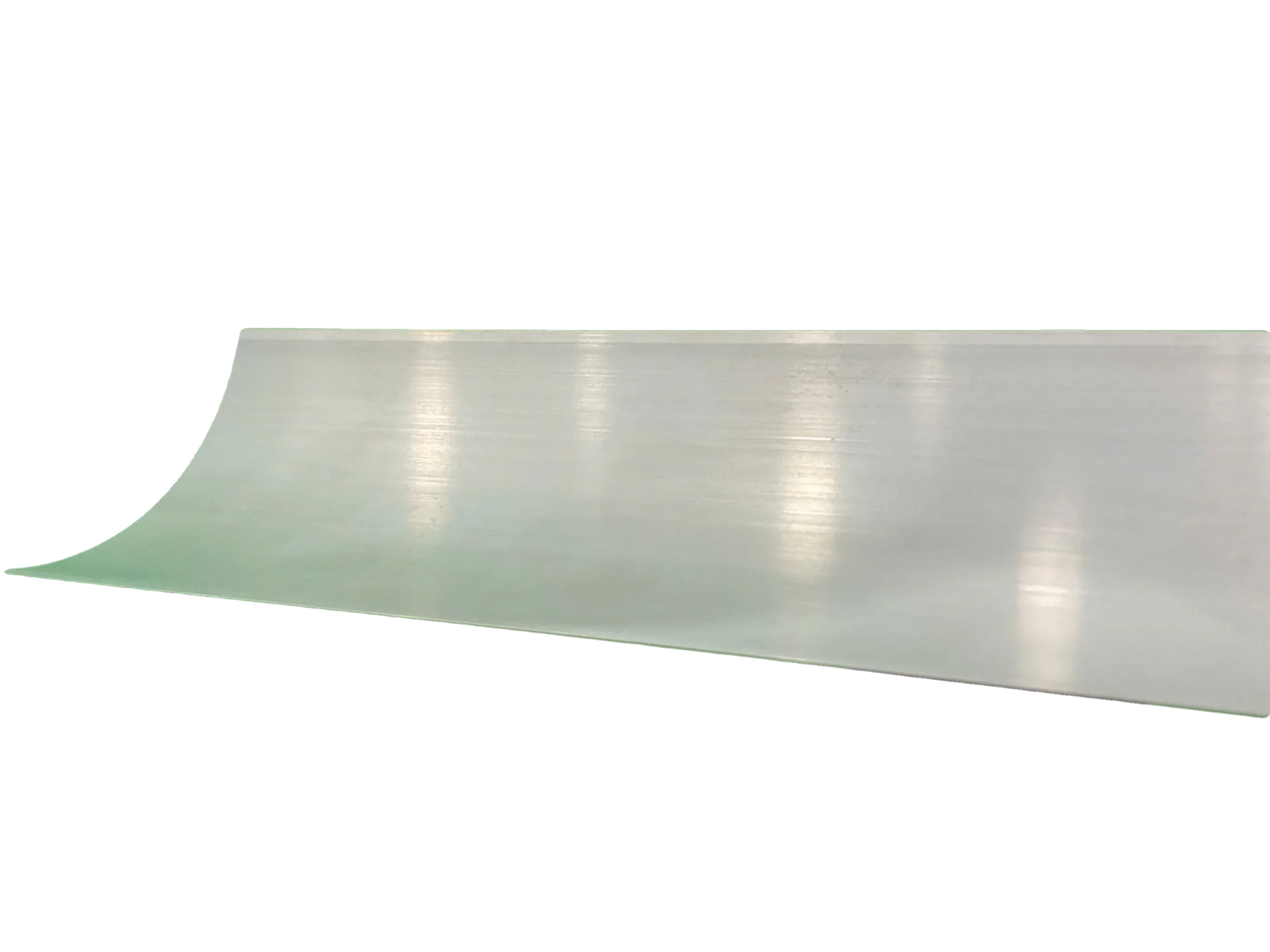
Enhanced Corrosion Resistance: Protection against the elements.
One of the most compelling benefits of anodized aluminum is its exceptional corrosion resistance. The thickened oxide layer acts as a formidable barrier, protecting the underlying aluminum from moisture, chemicals, and atmospheric pollutants.
This inherent protection reduces maintenance costs and extends the lifespan of your structures, ensuring long-term value and minimizing the need for costly replacements. This is particularly crucial in harsh industrial environments, where materials are subjected to constant wear and tear.
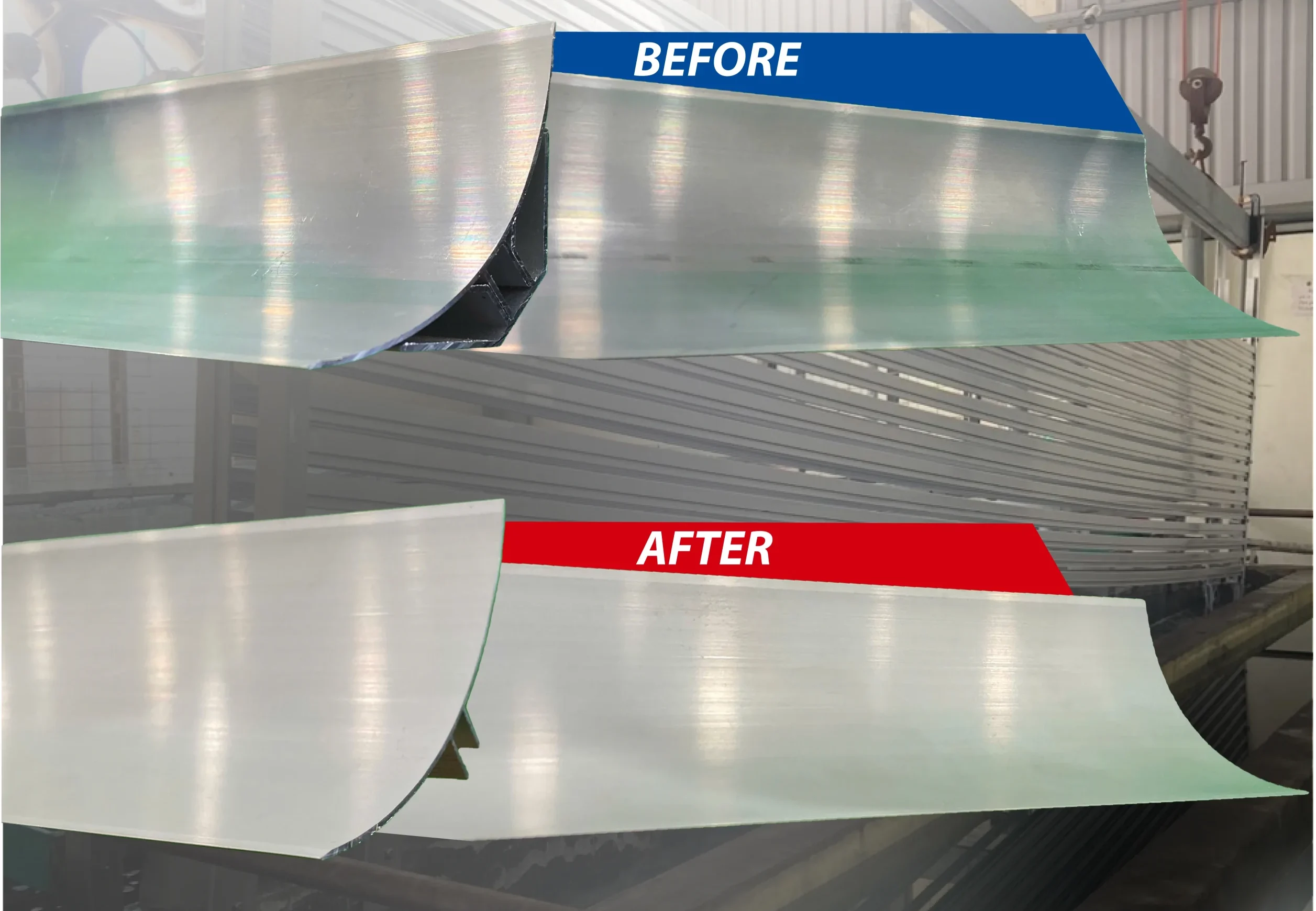
Increased Durability and Wear Resistance.
Anodized aluminum is significantly harder and more wear-resistant than untreated aluminum. This enhanced durability makes it ideal for high-traffic areas, exterior facades, and structural components that experience frequent abrasion. The hardened surface resists scratches, dents, and other forms of damage, preserving the aesthetic appeal and structural integrity of your buildings for years to come.
This inherent robustness translates to reduced maintenance and replacement costs over the lifecycle of your projects.
Improved Aesthetics: A variety of colors and finishes.
Anodized aluminum offers unparalleled design flexibility. The porous nature of the anodized layer allows for the incorporation of dyes, enabling a vast spectrum of colors and finishes. From vibrant hues to subtle metallic sheens, anodized aluminum can be customized to match your architectural vision and create stunning visual effects.
This versatility empowers architects and designers to realize their creative aspirations while maintaining the material’s exceptional performance characteristics.
Enhanced Functionality: Improved adhesion for paints and adhesives.
Beyond its aesthetic and protective qualities, anodized aluminum offers enhanced functionality. The anodized surface provides superior adhesion for paints, primers, and adhesives, opening up a world of possibilities for customization and integration with other building materials.
This enhanced adhesion ensures long-lasting finishes and facilitates the creation of complex assemblies, streamlining construction processes and enhancing design flexibility.
Exploring Different Aluminum Finishes: Anodizing vs. Other Surface Treatments
When considering anodized aluminum for your project, it’s essential to compare it with other surface treatments:
Anodizing vs. Powder Coating: Comparing Performance and Cost
While both anodizing and powder coating enhance durability and aesthetics, they differ significantly in application processes and results. Anodizing creates a chemical bond with the metal surface, providing superior corrosion resistance and scratch resistance compared to powder coating, which relies on a polymer-based finish that can chip or fade over time.
Feature | Anodizing | Powder Coating |
Durability | High | Moderate |
Corrosion Resistance | Excellent | Good |
Color Options | Wide variety | Limited |
Application Cost | Variable based on quantity | Generally lower |
Anodizing vs Painting: Understanding the trade-offs.
Painting aluminum can provide a wide range of color options, but it is susceptible to scratches, fading, and chipping. Anodized aluminum’s inherent color integration offers superior fade resistance and scratch protection, maintaining its vibrant appearance for years to come.
While painting may offer a quicker turnaround time, the longevity and reduced maintenance requirements of anodized aluminum make it a more cost-effective choice in the long run.
Anodizing vs. Metal Plating: Which is right for your application?
Metal plating, like chrome or nickel plating, can enhance corrosion resistance and aesthetics. However, plating can be susceptible to peeling and flaking, compromising both appearance and protection. Anodizing’s integral bond with the aluminum substrate ensures a more durable and reliable finish, especially in harsh environments.
While plating may offer specific advantages for certain applications, anodizing’s overall performance and longevity make it a preferred choice for many industrial construction projects.
Applications of Anodized Aluminum Across Industries
The versatility of anodized aluminum extends far beyond industrial construction, finding applications in diverse industries:
Architecture and Construction: Extrusions, panels, and curtain walls.
Anodized aluminum extrusions, panels, and curtain walls are becoming increasingly prevalent in modern architecture. Their sleek appearance, durability, and corrosion resistance make them ideal for facades, roofing systems, and other exterior applications. The ability to customize color and finish allows architects to create visually stunning structures that withstand the test of time.
Automotive and Aerospace: Performance parts and components.
The lightweight yet strong nature of anodized aluminum, combined with its corrosion resistance, makes it a preferred material in the automotive and aerospace industries. From engine components to aircraft parts, anodized aluminum provides crucial performance advantages while minimizing weight and maximizing durability.
Consumer Goods: Cookware, electronics, and sporting goods.
Anodized aluminum finds its way into a multitude of consumer products. Its durability and resistance to scratches and wear make it ideal for cookware, electronic casings, and sporting equipment. The ability to customize color and finish also enhances the aesthetic appeal of these products.
Industrial Applications: Machinery and equipment.
Anodized aluminum’s robust properties make it well-suited for various industrial applications. From machinery housings to specialized equipment components, anodized aluminum provides protection against corrosion, wear, and tear, ensuring reliable performance in demanding environments.
Choosing and Maintaining Anodized Aluminum Products
Selecting the right anodized aluminum product and implementing proper maintenance procedures are essential for maximizing its benefits:
Selecting the right alloy and finish for your project.
Choosing the correct aluminum alloy and anodizing finish is crucial for achieving optimal performance. Factors to consider include the specific application, environmental conditions, and desired aesthetic outcome. Consulting with Cozydoor’s experts will ensure you select the ideal anodized aluminum solution for your unique project requirements.
Finding reputable Anodizing Services and Suppliers.
Partnering with a reputable anodized aluminum supplier is essential for ensuring quality and reliability. Cozydoor boasts extensive experience and expertise in providing high-quality anodized aluminum products and services. Our commitment to customer satisfaction and our stringent quality control measures guarantee that you receive superior products that meet your exact specifications.
Caring for anodized aluminum: Cleaning and maintenance tips.
Proper maintenance can significantly extend the lifespan of your anodized aluminum products. Regular cleaning with mild soap and water is typically sufficient to remove dirt and grime. Avoid abrasive cleaners and harsh chemicals, as they can damage the anodized surface. Cozydoor provides detailed care instructions to help you maintain the beauty and performance of your anodized aluminum for years to come.
Cozydoor’s anodized aluminum empowers you to transcend the limitations of traditional building materials. Elevate your industrial construction projects with enhanced durability, stunning aesthetics, and unparalleled performance. Contact us today for a personalized consultation and unlock exclusive pricing. Let Cozydoor be your trusted partner in achieving construction excellence.


